Food/Beverage

-Retort.jpg)
In fall 2024, JBT Marel launched a first-of-its-kind, patented Efficient Agitation (EA) Retort technology that now offers customers significantly more versatile packaging capabilities. Specifically, it’s designed for food packaging and preservation needs across several ready-to-eat and ready-to-drink food markets, from coffee and milk products, to baby food, frozen produce, and soups. Products being processed by the EA Retort are gently agitated while being heated to FDA required temperatures to become shelf-stable and safe for consumption.
JBT Marel’s EA Retort offers a different way to safely package foods versus traditional retort agitation. For example, unlike trademarked traditional steam water spray (SWS) static retort, the JBT Marel EA Retort offers a patented trapezoidal motion, providing a greater mix energy in a shorter stroke length during the sterilization process. The result is that more versatile packaging options can now be used in retort processing - such as cartons, aluminum cans, and glass jars. Simply put, the innovative EA Retort technology expands manufacturers’ options for sustainable and environmentally friendly packaging that is increasingly in demand by both consumers and industry leaders by using gentler processes for more delicate packaging solutions, all while providing better taste and texture to the food. Prior retort agitation technologies could not accommodate certain sustainable packaging materials, like liquid paperboard containers. The EA retort is also able to seamlessly integrate into facilities already using these materials. This opens the door for manufacturers who are looking to make the switch to environmentally friendly solutions.
Unique to JBT Marel, the EA Retort features qualities like the space-saving vertical door option, maximizing productivity in smaller facilities, and the SuperStatic capabilities of the Steam Water Spray (SWS) System, ensuring uniform and efficient thermal processing to boost product quality.
The EA Retort also keeps efficiency top of mind throughout each stage of production. In addition to the quick heating capabilities and the vertical door option for compact spaces, the technology allows products to be packaged more tightly and with less brine. For example, lighter packages can lay flat in shipping containers, which maximizes shipping space while still ensuring the delivery of fresh, ready-to-eat/drink products.
What makes your product or technology innovative?
JBT Marel’s one-of-a-kind EA Retort redefines retort agitation with its perfect balance between static processing and agitation.
The patented technology of the EA Retort is innovative because it surpasses traditional retort agitation by offering more packaging flexibility and quicker heating capabilities, resulting in ready-to-eat and drink products that are better in quality from a taste and texture standpoint. Unique advanced linear agitation technology is used to produce more consistent results than traditional retort agitation, while reducing sterilization cycle times by up to 43% for shelf-stable goods.
The EA Retort brings goods to FDA required temperatures up to 30% faster than traditional retort agitation, and can speed cooling times by up to 34%. This reduces utility costs and the number of retorts required for production, while contributing to sustainability benefits by lowering energy usage in facilities using the technology.
This product offers both a unique solution for manufacturers, and several benefits for the end-consumer. Shorter sterilization cycles result in higher-quality packaged goods with fresher tastes and textures.
JBT Marel’s EA retort is gentler on sustainable food packaging systems than traditional rotational agitation, and the technology’s infinitely customizable programming adjusts to a variety of packaging options, from pouches, aluminum cans, bottles, cups and bowls, giving users the option to pursue more sustainable solutions. These packaging choices also allow consumers to take advantage of local recycling programs. Additionally, reduced operation costs can trickle down to the consumer to make fresh, sustainable products more accessible than ever.
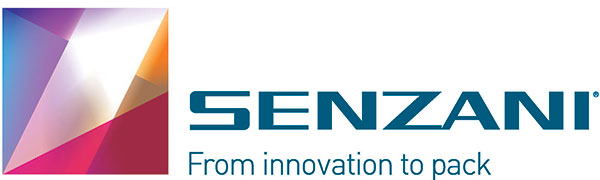
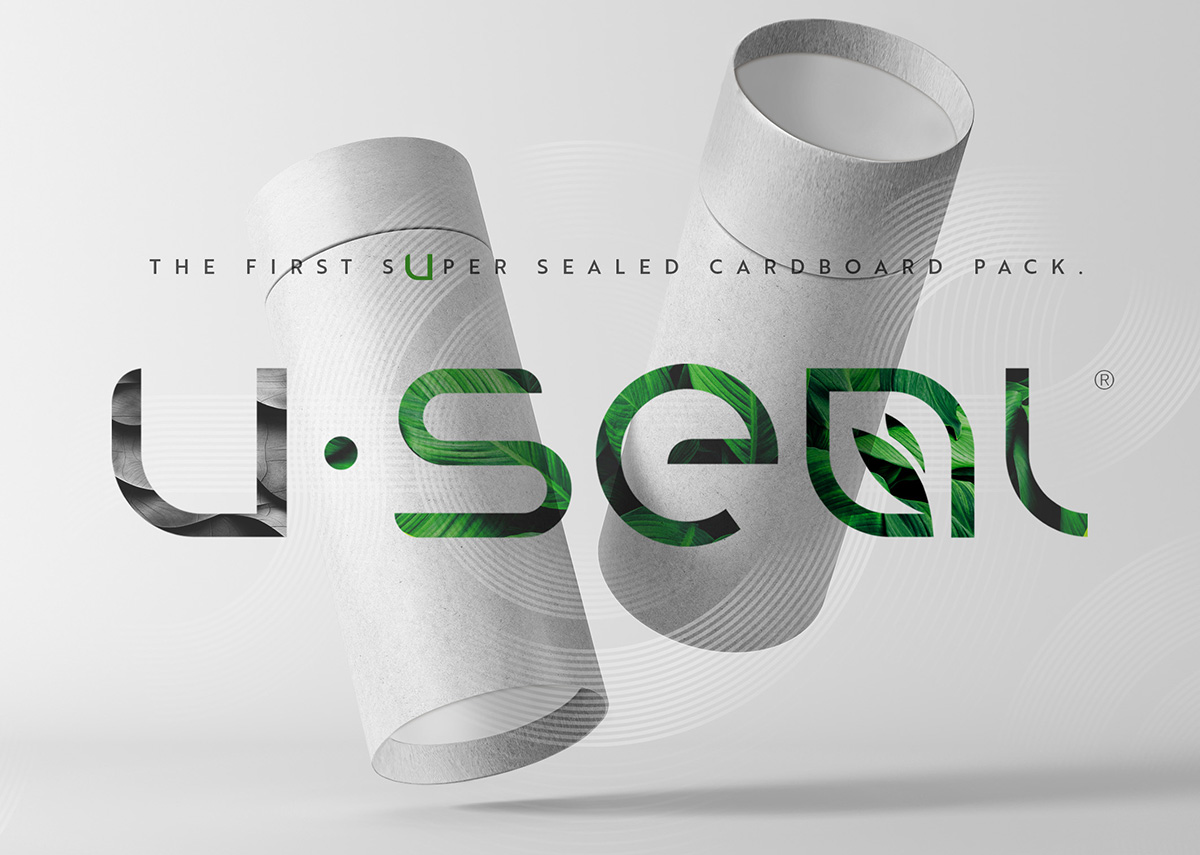
U-Seal is a patented cold-sealing technology developed by Senzani Brevetti that redefines the standards of cardboard packaging. Designed to meet the evolving needs of marketing and sustainability across a wide range of industries, U-Seal enables the creation of fully recyclable cardboard packs in a wide variety of unique, eye-catching shapes, all starting from a flat blank.
This ability to produce packs starting from flat blanks makes U-Seal a sustainable technology, as it not only optimizes warehouse space management, but also improves transport efficiency, consequently reducing emissions and environmental impact.
In addition, the fact that all packs are made of cardboard material adds to the sustainability aspect of this solution, helping companies in their transition towards more sustainable packaging options, without compromising on design.
In fact, U-Seal also opens a world of opportunities concerning the shelf appeal of the end product, making brands stand out thanks to the wide variety of shapes which can be produced, such as packs with circular, oval, triangular, square, and hexagonal bases.
Further customization opportunities include handling of packs with different diameters and heights and the possibility of adding features such as transparent windows for product visibility, tamper-evident systems like tear-strip openings, dispensing lids, as well as the option of having high-impact printing both on the inside and outside of the pack and different barrier levels for product protection.
U-Seal allows for maximum safety and efficiency in the production facility: thanks to the patented cold-sealing technology, it reduces both the risks to operators and the time required to safely access the machine in the event of a downtime. The system supports production speeds ranging from 20 to over 300 packs per minute, thanks to its modular and customizable configuration, which includes three core components: the Former, Filler, and Closer. These modules can function independently or as a compact 3-in-1 solution, depending on customer requirements.
Already making an impact on a wide range of industries, including confectionery, pet food, coffee and tea, cereals, home and personal care, and tobacco, U-Seal represents a significant advancement in modern packaging technology. With its combination of performance, safety, and sustainability, it is a future-ready solution that empowers companies to innovate without compromise.
What makes your product or technology innovative?
Senzani U-Seal revolutionizes the packaging world by combining cutting-edge technology, high performance and sustainability, while allowing for complete creative freedom in pack design.
The core of this solution is the patented cold sealing technology, which significantly enhances operator safety and allows for quicker machine access in case of downtime, compared to conventional heat-based technologies.
At the same time, U-Seal supports eco-friendly practices. The system’s ability to produce tightly sealed packs using fully recyclable cardboard aligns with modern sustainability goals. Moreover, producing all packs starting from flat blanks reduces logistical footprints through efficient storage and transport, consequently reducing environmental impact.
From a technical standpoint, U-Seal delivers exceptional speed and precision, packaging up to 330 units per minute with exceptional sealing quality. Its modular design gives manufacturers the flexibility to scale and adapt to their production needs.
Finally, U-Seal offers a level of functional and aesthetic customization that sets it apart from any other solution on the market. Its ability to form and seal packs in a wide range of outstanding shapes and sizes makes U-Seal a marketing powerhouse. Additionally, U-Seal supports advanced packaging features such as transparent windows, tamper-evident systems, dosing lids, custom printing both on the inside and outside of the pack, and product-specific barrier levels, making it adaptable across diverse sectors including food, pet food, home & personal care, and more.
In essence, U-Seal is not just a packaging solution; it’s a strategic tool that aligns with modern demands for sustainability, customization, and operational efficiency.
.jpg)
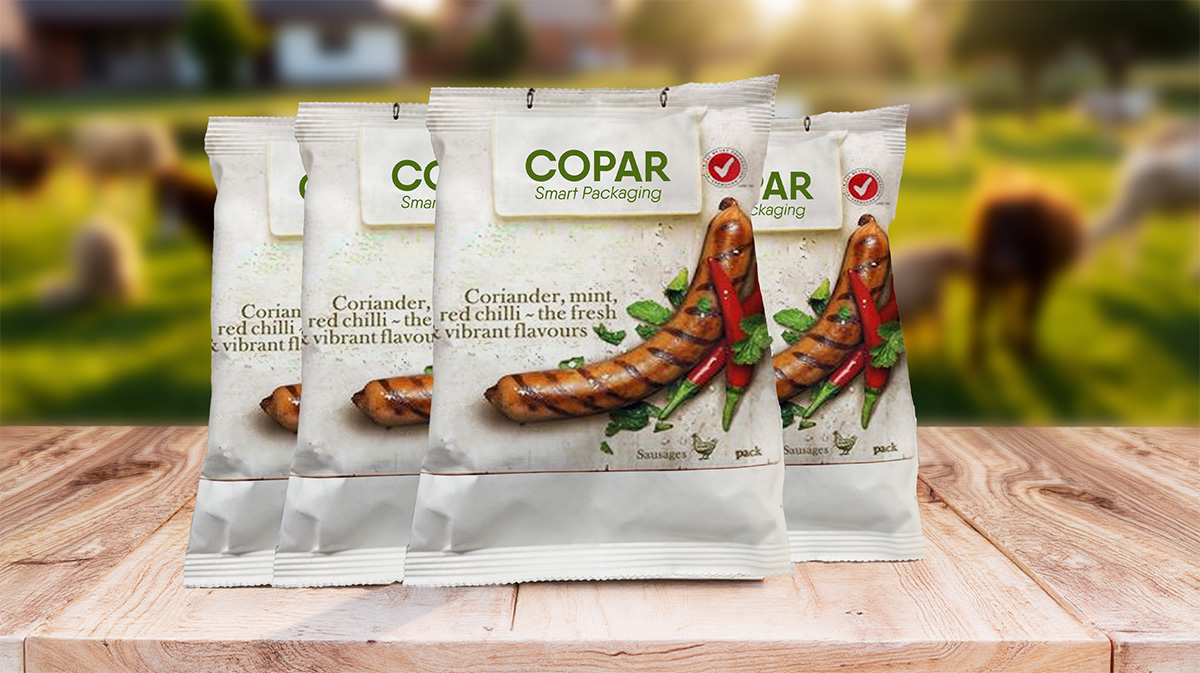
Hyper Barrier™ paper by Copar, developed in collaboration with Smart Planet Technologies, is a next-generation packaging material designed to replace complex multilayer plastic laminates in food and beverage applications. Using a single layer of commodity polymer (HDPE/LDPE) enhanced with nanocomposite barrier technology, Hyper Barrier™ delivers 200–400x better oxygen barrier and 5–7x better moisture barrier than traditional PE coatings—without the need for costly polymers like EVOH or foil.
This innovation fills a critical market gap: enabling high-performance barrier packaging without the environmental and cost drawbacks of multilayer plastics. Hyper Barrier™ provides the “just-right” level of protection required for sliced meats, dry foods, frozen items, and flow wraps—while maintaining recyclability in standard recycling streams.
It empowers food and beverage brands to significantly reduce plastic use, simplify material structures, and meet growing demands for sustainable packaging. Hyper Barrier™ helps brands avoid plastic taxes, align with global sustainability mandates, and comply with extended producer responsibility (EPR) and recyclability assessment (RAM) standards across the UK and EU.
Commercially scalable and production-ready, Hyper Barrier™ integrates seamlessly into existing converting and filling lines, making it accessible to operations of all sizes. It delivers the performance of traditional high-barrier laminates with the environmental profile and cost-efficiency of recyclable paper.
It is engineered to support compliance with global packaging regulations, including UK Plastic Packaging Tax, EPR (Extended Producer Responsibility), and RAM (Recyclability Assessment Method) criteria in the UK and EU. This makes it easier for brand owners and converters to meet evolving sustainability targets and avoid penalties without compromising on performance.
Hyper Barrier™ Paper is also designed as a drop-in solution—compatible with existing converting, and filling equipment—making it both technically and economically scalable. This removes many of the barriers associated with switching from plastic to paper and simplifies the adoption of circular design principles.
What makes your product or technology innovative?
Hyper Barrier™ paper by Copar, developed with Smart Planet Technologies, is a packaging innovation engineered specifically for food and beverage applications. It replaces multilayer plastic laminates with a single-layer nanocomposite barrier coating on paper, using commodity polymers (HDPE/LDPE) to achieve 200–400x better oxygen barrier and 5–7x better moisture barrier than traditional PE coatings—without using costly EVOH or foil.
Food products like sliced meats, cheese, coffee, dry mixes, and frozen items demand strong barrier protection—but current high-performance laminates are expensive, hard to recycle, and often over-engineered. Hyper Barrier™ delivers the “just-right” level of protection for these applications, keeping food fresher for longer while significantly reducing packaging complexity and plastic content.
Its performance is matched by practicality: Hyper Barrier™ is a drop-in solution that runs on existing converting and filling lines without special handling. It is commercially scalable and designed to reduce material costs while improving shelf life and sustainability metrics.
Importantly, Hyper Barrier™ is recyclable through standard recycling streams—meeting the dual need for performance and environmental compliance. It helps food brands meet plastic reduction goals, avoid packaging taxes, and comply with EPR and recyclability regulations across global markets.
Hyper Barrier™ deserves recognition for redefining what’s possible in food packaging: robust barrier performance, reduced plastic, and full recyclability—all in a format that is affordable, scalable, and aligned with the needs of modern food producers and consumers.
General Packaging & Processing

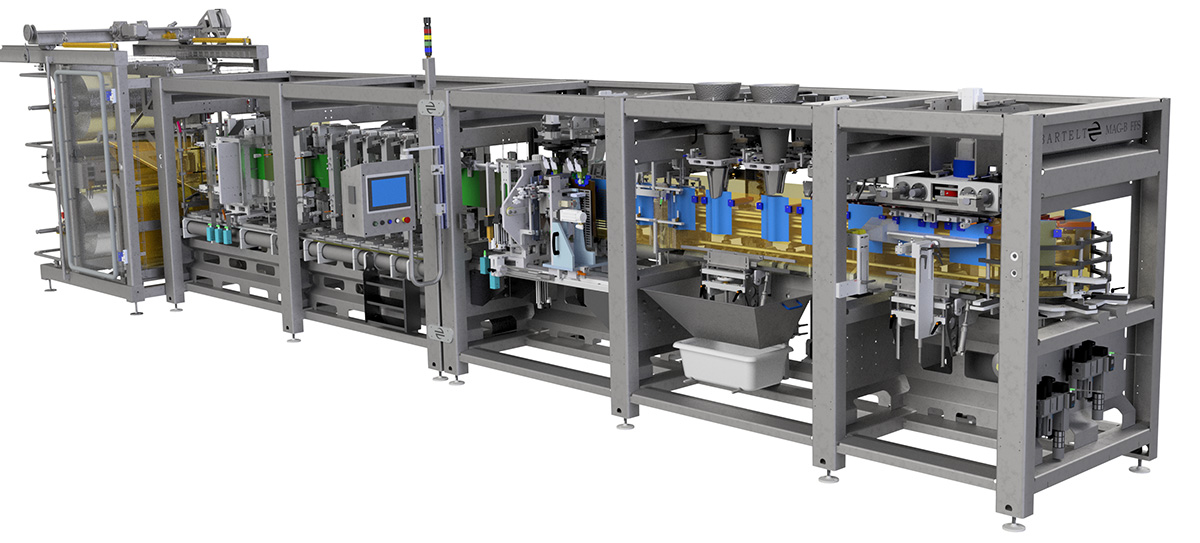
The Bartelt MAG-B Horizontal Form Fill and Seal machine is the next-generation solution that will transform your pouch packaging production through innovative magnetic track motion, pitch-less operation, and unmatched changeover efficiency. As part of Bartelt’s MAG Series, the MAG-B is built for manufacturers who need fast, reliable changeovers, sustainable material compatibility, and long-term flexibility—all within a clean and low-maintenance platform.
At its core, the MAG-B features a magnetic track system, replacing traditional mechanical chains and belts with smooth, contactless motion. This enables true pitch-less operation, allowing users to quickly switch between bag sizes and formats without the manual adjustments required with mechanical spacing. During changeover, the Adaptive Sealing Control automatically adjusts the sealing and cooling bar assemblies to the correct position, including compensation for film stretch, a common challenge when using recycle-ready materials. The result is faster changeovers, fewer wear parts, and greater agility for high-mix production environments.
Also unique to the MAG-B is Bartelt’s patented magnetic pouch clamp system to securely handle a wide range of film substrates. These clamps are maintenance-free – not using mechanical springs, bushings or linkages that you will find in competitive designs - significantly increasing uptime and operational efficiency.
The MAG Series consists of four distinct models, each offering specific advantages which allow processors to choose the optimum machine for their footprint, throughput, and application needs. Features such as zipper modules, film splicers, nitrogen flushing, and eco-film compatibility can be added to any model without overhauling the core system.
The MAG-B delivers in sanitary performance with a clean, open design, and an IP69K-rated washdown magnetic track, which is ideal for food and personal care environments where hygiene is critical.
Built with advanced automation, the MAG-B incorporates intuitive, recipe-based controls, precision servo-driven motion, and an efficient film handling systems that reduce scrap and optimize roll yield. It is also engineered to run recyclable and mono-material films—empowering manufacturers to meet their sustainability targets without compromising performance or throughput.
For manufacturers aiming to upgrade their pouch packaging lines, the MAG-B has been specifically engineered to minimize the collateral costs linked to the replacement of outdated pouchers. The linear track provides the flexibility to adjust the filling position to align with current scale chute locations, while also presenting options for both right- and left-hand configurations. The MAG-B decreases downtime, promotes the use of more sustainable materials, and can be scaled over time; it offers unparalleled speed, ease of use, and versatility in the industry.
What makes your product or technology innovative?
Bartelt’s MAG-B redefines what’s possible in HFFS pouching technology through three industry-first innovations: a space-efficient magnetic track system, a patented, maintenance-free pouch clamp design and Adaptive Sealing Control which automatically adjusts sealing and cooling assemblies during changeover, including compensation for film stretch.
Traditional pouching machines rely on fixed mechanical drives, timing chains, and manual adjustments, limiting flexibility and creating wear points, increasing downtime and maintenance. Additionally, they lack the flexibility to quickly adapt to different product configurations.
Bartelt’s MAG-B’s allows one operator to perform a changeover on the fly without mechanical adjustments in less than 15 minutes. Additionally, the MAG-B is configured to utilize the front and rear of the track providing world-class functionality in a compact footprint and cycle rates that can exceed 150 PPM.
The magnetic track allows an exclusive product settling "shake" feature at filling and purging, which reduces O2 levels and obtains better product settling.
These capabilities, combined with Bartelt’s patented maintenance-free pouch clamps, result in a machine platform uniquely designed to meet your current and future production needs. When future requirements require different sizes, faster production, or the integration of mono-materials and/or thin-gauged substrates, the MAG-B is designed with the capability to adapt quickly and efficiently.
Together, these innovations provide a powerful combination of speed, flexibility, and reliability that set the MAG-B apart from conventional HFFS machines.
In an industry driven by SKU proliferation, labor challenges, and sustainability goals, the MAG-B delivers future-ready performance and adaptability—helping manufacturers stay competitive today and prepared for tomorrow.
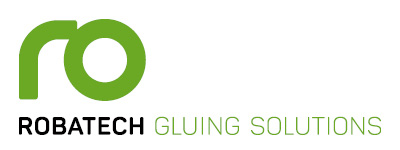
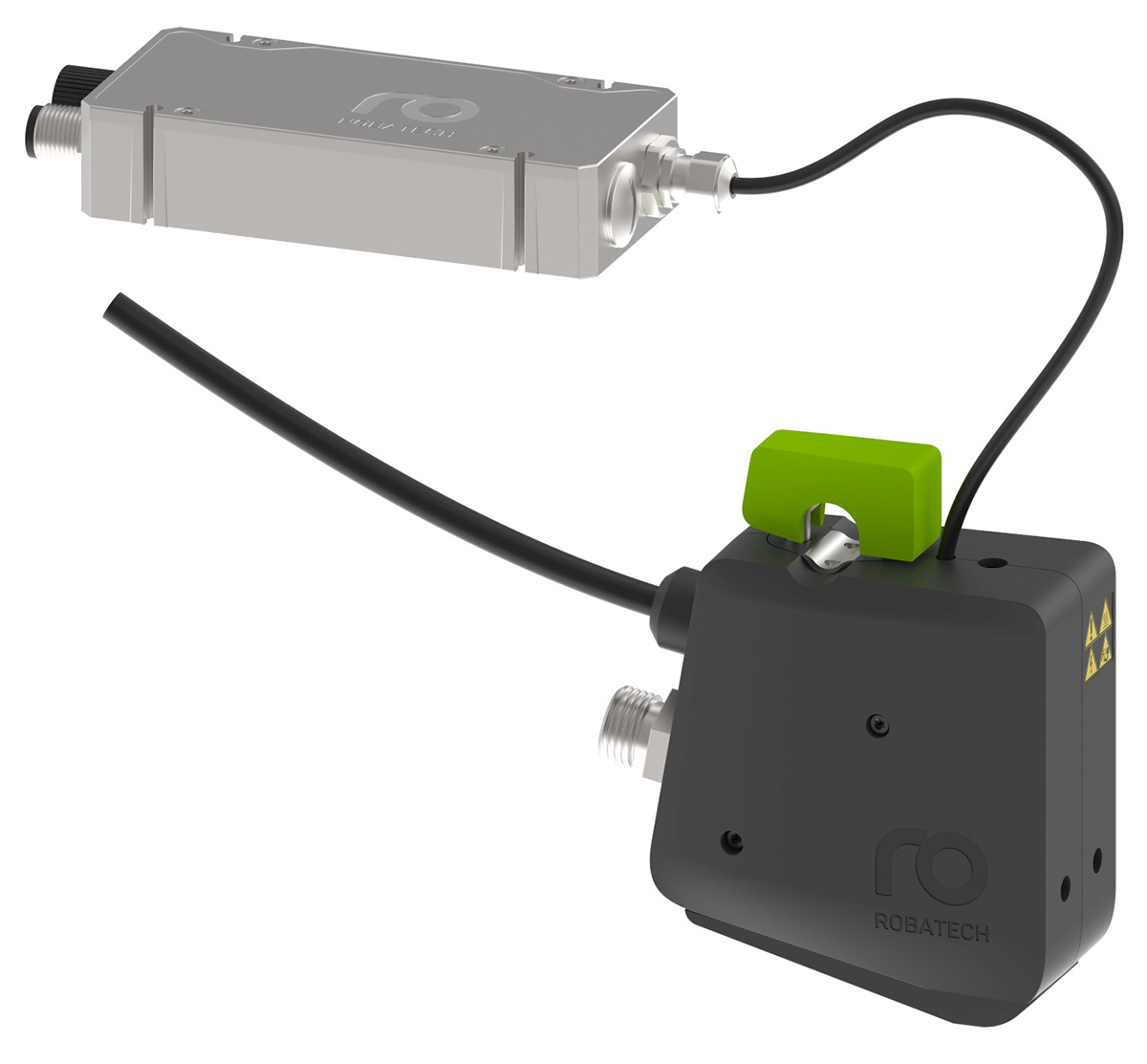
Robatech's innovative Volta electronic adhesive jetting head is redefining the benchmarks in adhesive application technology. This advanced head is distinguished by its impressive warranty covering 2 billion lifetime cycles, underscoring both its durability and reliability. Additionally, its all-electric design eliminates the need for compressed air, thereby promoting significant reductions in energy consumption and enhancing sustainability in industrial processes. Energy savings by as much as 60% has been observed compared to pneumatically operated heads.
The new Volta head also introduces an innovative integrated pattern control, allowing for direct programming on the head itself—a significant advancement in adhesive application technology. For instance, if a customer wishes to switch from applying beads to dots of adhesive on their packaging, the head enables programming the specific number of dots without relying on the adhesive melter, which has been the conventional approach. This advancement not only enhances the versatility of the Volta head in relation to Robatech adhesive melters but also extends its applicability to any adhesive melter available on the market, highlighting its importance in streamlining and improving operations.
Main customer benefits include:
- 60 % less energy consumption than pneumatic jetting heads
- Save up to 40% to even 50% adhesive with hotmelt stitching
- Electric application head for high process reliability
- Low maintenance and robust due to absence of dynamic seals
- Reduced downtime due to longer service life of 2 billion operating cycles
- Repeatable and precise beads and dots for fast applications up to 200 Hz
- Easy system integration via 24 VDC (3-wire) connection without booster
- CoolTouch insulation protects personnel from burns, protects heat-sensitive products, and reduces energy consumption
- Increased ingress protection IP55 as standard function at no extra cost
- Lower operating costs and reduced module maintenance by eliminating compressed air and dynamic sealings
What makes your product or technology innovative?
Robatech's innovative Volta adhesive application head introduces a groundbreaking standard with its 2 billion cycle lifetime warranty, underscoring a significant advancement in the industry. This head is equipped with an integrated pattern control module, enabling end users to precisely dictate the adhesive application directly from the head, a pioneering feature never before seen in the adhesive technology sector. Traditionally, such pattern controls required programming from the adhesive melter or through an external interface. Furthermore, the Volta head demonstrates exceptional compatibility, functioning seamlessly with not only Robatech adhesive melters but with any adhesive melter available on the market, broadening its utility and impact across various industrial applications.
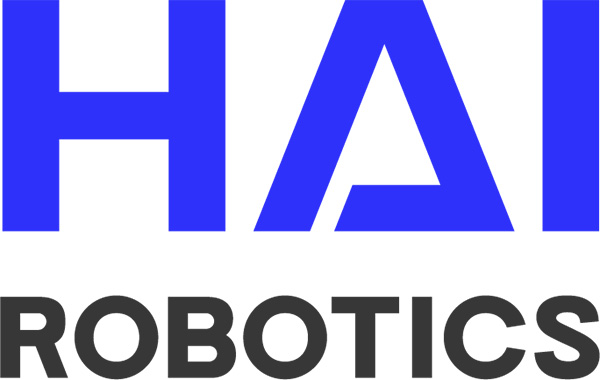
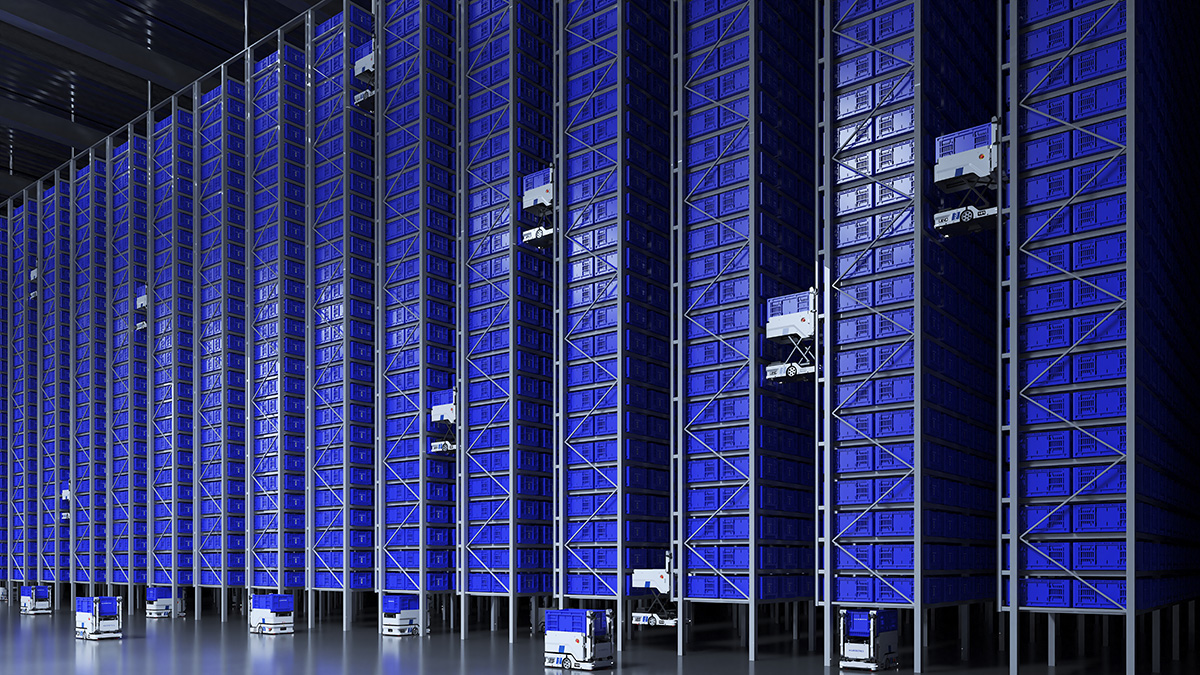
The HaiPick Climb System revolutionizes automated storage and retrieval systems (ASRS) with its HaiClimber robot, the first of its kind to climb warehouse racks and operate in low-precision environments. This enables broader automation access for businesses and maximizes use of existing facilities.
Unlike traditional ASRS, the system works with standard racking and totes that can be locally sourced around the world, eliminating the need for costly, high-precision setups. Components can be sourced locally, easing implementation and compliance worldwide.
The robot climbs via just two channels on one side of the racking—reducing maintenance and improving reliability. With speeds of 4 m/s and direct bin access, it delivers orders 34% faster than typical ASRS. Its ability to move freely in all directions eliminates aisle congestion and ensures smooth, efficient workflows.
What makes your product or technology innovative?
The HaiPick Climb System is advanced technology that is simplifying automation while expanding what can be expected from automated storage and retrieval systems (ASRS). The system is operated by the first warehouse climbing robot, HaiClimber, with the ability to easily navigate low precision environments, making inventory automation possible for more businesses and helping companies get more from their existing facilities. It frees facilities of the burden, time, and costs typically required of robotic solutions, breaking down barriers to warehouse advancement and lower the cost of automation ownership for all facilities.
HaiClimb Systems can be constructed of almost any industry standard racking and storage containers, eliminated the high cost, extreme precision, and limitations that are typical of historic ASRS solutions. Totes and racking can be sourced locally around the world, simplifying implementation and making local compliances even easier.
The compact robot climbs on 2 channels connected to 1 side of the racking, half the connection points of typical ASRS climbing technology, creating a more reliable climb and simplifying maintenance.
Travelling at extreme speeds of 4 meters/second, and with direct access to each bin at all times, orders can be delivered to picking stations in only 2 minutes after order intake – 34% faster than typical ASRS. Each HaiClimber robot is able to freely navigate under reaching in any direction, allowing each robot to take the most efficient path to inventory and workstations, preventing robotic “traffic jams” caused by aisle-only travel and ensuring consistently fast operations.
Personal Care/Pharma
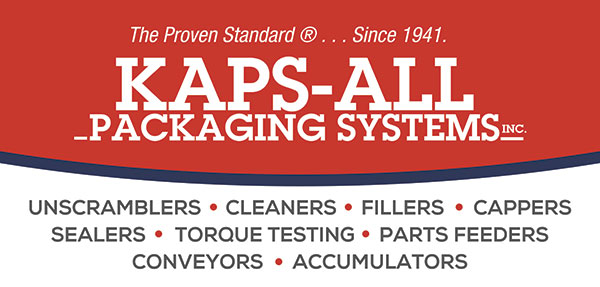
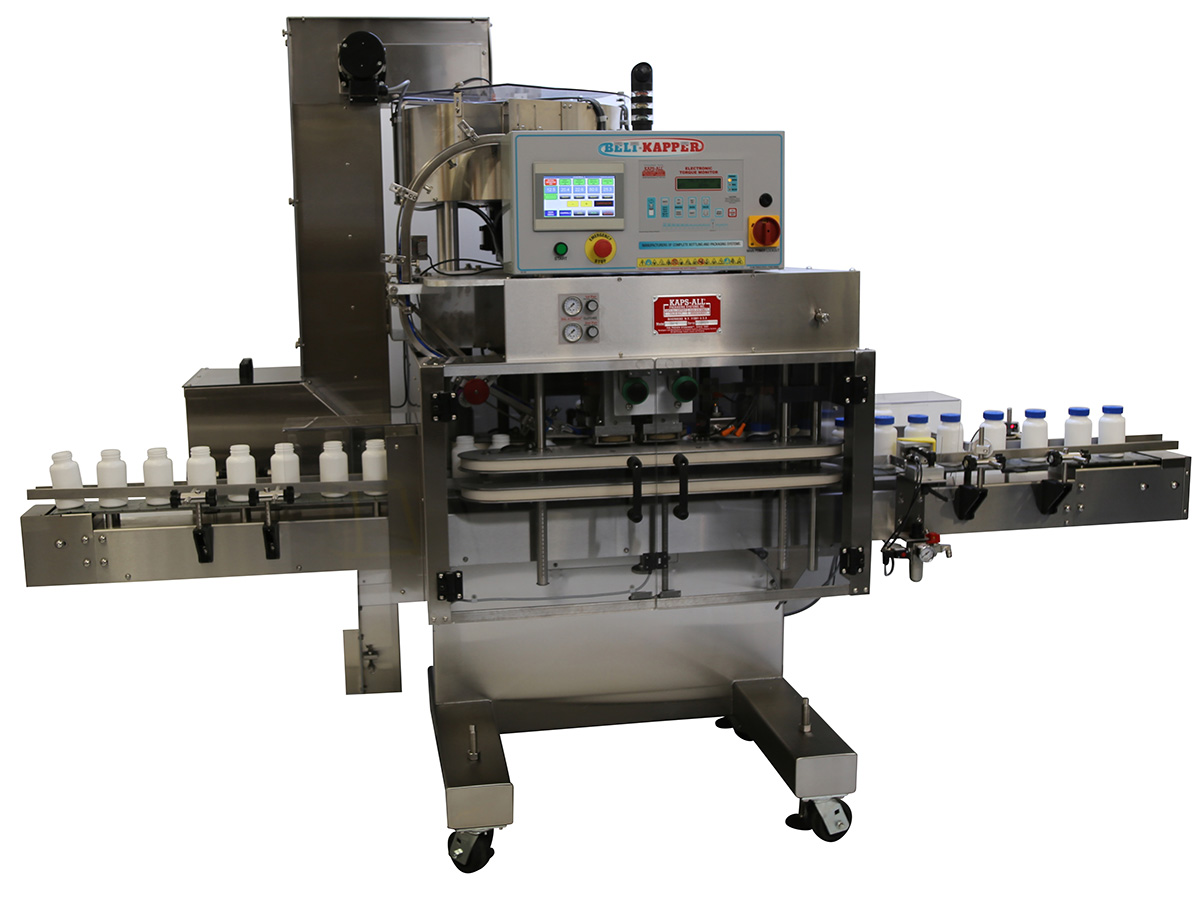
The Kaps-All BK-4 Belt Capper is a high-performance, GMP-compliant capping solution engineered for the stringent requirements of the pharmaceutical and cosmetics/personal care industries. Designed for precision, flexibility, and line efficiency, the BK-4 is ideal for applications ranging from fragile vials to 14+ inch tall bottles, handling closures from 13 mm to 70 mm diameter.
At the heart of the BK-4’s innovation is its 4-belt clutched cap tightening system. This patented configuration uses independent adjusting belt assemblies to gently but firmly grip the closures while applying torque without scuffing, over-tightening, or damaging delicate closures or high-finish cosmetic packaging. The belts automatically adjust to varying diameters and shapes, accommodating everything from squeezable plastic to rigid glass, all while maintaining exceptional capping accuracy. While both spindle and belt style cappers both offer pros and cons, we are the first manufacturer in the space to offer both solutions recognizing the benefits of each.
Built on a stainless steel frame, the BK-4 is capable of being fully washdown-compatible and supports tool-less changeovers, aided by motorized head-height adjustment, screw-style guide belt control, and digital linear encoder positioning with speed feedback. Operators benefit from a user-friendly color touchscreen HMI that includes recipe recall, multilingual support, event logging, password protection and much more—ideal for regulated environments where operator traceability and repeatability matter.
What further sets the BK-4 apart further is its integration with the EM-980 Torque Tester, an inline, real-time monitoring system that ensures every cap is applied within spec. The EM-980 displays live torque data in 0.1 lb-in increments, records statistical metrics (min, max, average, standard deviation etc.), and alerts operators instantly if a closure falls outside acceptable limits. The BK-4 comes with an integral reject system to ensure only tested and verified components are sent downstream from the capping station. This level of in-process verification helps ensure compliance with stringent audit requirements without manual testing or delays, capable of analyzing 200 readings per minute even.
The EM-980 also provides outputs for printing and computer data collection, enabling full torque data integration into simple spreadsheets or 3rd party systems. With options such as flashing alarms, reject paddles, and label printers, the unit can fully automate rejection of non-compliant products helping maintain packaging aesthetics and avoid errors.
Together, the BK-4 and EM-980 deliver a robust capping solution that prioritizes precision, consistency, and hygiene, while enhancing productivity in high-speed filling lines. Whether it’s a tamper-evident cap on a medical tincture or a polished closure on a luxury serum bottle, the BK-4 provides the performance and adaptability modern manufacturers demand with inline quality assurance built right in.
What makes your product or technology innovative?
The BK-4 Belt Capper with EM-980 Torque Monitor is an innovative leap forward in hygienic, compliant, and quality-focused packaging for the pharmaceutical and cosmetics/personal care industries.
While many cappers rely on disc-based mechanisms that struggle with closure variability or risk damaging high-end packaging and limited contact with the caps. The BK-4 uses a patented 4-belt system that gently yet precisely grips each closure minimizing scuffing while achieving consistent torque across cap styles from standard caps to child resistant caps and beyond. This flexibility is critical for brands seeking to maintain aesthetic integrity in luxury cosmetics and dosage integrity in pharma.
What truly sets this system apart is the EM-980 Torque Monitor, an inline, electronic quality control unit that measures and records cap torque in real time on every bottle. Unlike traditional torque testers that rely on offline sampling, the EM-980 provides 100% inline verification, immediately alerting operators and/or rejecting under/over-torqued closures. This not only ensures 100% torque compliance but also streamlines operations, reducing manual inspection and rework.
The BK-4 also incorporates on-board inspection for verification of missing cap, missing foil, crooked cap etc. This is incorporated into the on-board reject system that is standard to this model. Its compact design, and seamless integration with the capper allow it to fit into space-constrained production lines. The result is a high-throughput, data-driven, operator-friendly capping solution that delivers premium results both in quality and appearance. For pharma and beauty brands looking to future-proof their packaging lines, the BK-4 with EM-980 is truly best-in-class.

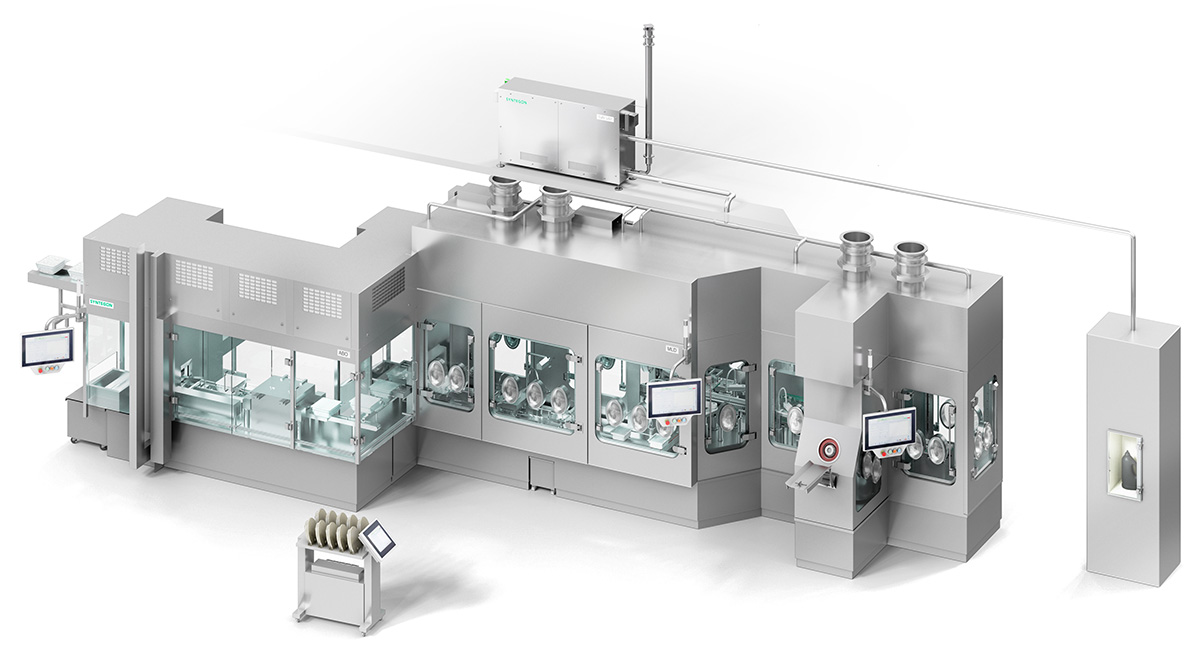
The MLD Advanced meets the increasing requirements of pharmaceutical manufacturers for high output with 100 percent in-process control (IPC). “Especially with high-value medicines, it is essential that each drop is filled and weighed optimally,” explains Markus Burkert, Product Manager at Syntegon. “That's why we have combined the MLD platform, which was previously used primarily for cartridges and vials, with our technologies for syringe filling.”
The automatic bag and tub openers, well-known from many syringe lines, use no-touch transfer to ensure the aseptic transfer of the syringes into the filling area. The Pharma Handling Unit developed by Syntegon denests the syringes automatically without glass-to-glass contact and places the containers into the pitch adjustment station. Here, the syringes are moved into the machine pitch and then placed in the clips of the machine transport. “This unique clip system is the first key feature we adopted for syringe applications from the cartridge line,” Markus Burkert explains. “The special circulating transport system ensures smooth transportation and is therefore ideal for RTU syringes, as well as vials and cartridges.
The empty syringes are weighed using 100 percent IPC, before they are transferred to the filling station. The subsequent filling and stoppering process is based on the proven FXS series for syringes: the filling needles are mounted on the Pharma Handling Unit and allow for flexible redosing if required. Thanks to IPC, the filling weight is controlled precisely. “In addition to minimizing product loss, an important focus is on providing documented proof about the weighing of each container. This gives manufacturers the certainty that all containers have been filled correctly,” explains Klaus Ullherr, Senior Product Manager at Syntegon. After stopper insertion via vacuum or vent tube, the containers are returned by the circulating transport system and gently placed in the nests by the Pharma Handling Unit. “This way, we can offer our customers a seamless process for their pre-sterilized syringes from a single source,” says Klaus Ullherr.
Customers benefit from this innovative combination of proven technologies in several ways: in addition to achieving an output of up to 400 syringes per minute, they also receive safe and proven processes. “By using tried and tested technologies, the machine is available quickly, and the risk is significantly reduced,” Markus Burkert underlines. The first customer is already convinced: the first MLD Advanced will soon be ensuring gentle processing and filling of RTU syringes with 100 percent IPC at a European pharmaceutical manufacturer.
What makes your product or technology innovative?
The prevalence of ready-to-use (RTU) containers in pharmaceutical manufacturing is growing rapidly. This is not surprising, as they reduce the number of manufacturing steps, minimize contamination risks, and provide higher efficiency and flexibility in production processes. Syntegon’s latest technology launch, the MLD Advanced, answers the high throughput, precise filling and stoppering needs of pharmaceutical manufacturers, with outputs of up to 400 RTU nested syringes per minute. By combining proven technologies on a new platform, customers benefit from tried and tested processes, faster availability, and reduced risk.
Syntegon has been developing fill-finish equipment for RTU containers for many years and understands production pain points: especially with high-value medicines, it is essential that each drop is filled and weighed optimally. Therefore, the new MLD Advanced is equipped with 100 percent in-process control (IPC), which enables flexible redosing and ensures maximum product yields without a reduction in speed. In addition, manufacturers receive documented proof confirming the accurate filling and stoppering of each container.
Further technological highlights include automatic bag and tub openers with no-touch transfer, the gentle, patented clip system with circulating transport and Pharma Handling Units to de- and re-nest syringes automatically without glass-to-glass contact while ensuring precise filling.
Feedback from the industry is very positive and multiple orders have already been placed. Pharmaceutical manufacturers are convinced that this innovative concept combines the best of reliable technology with new innovations and Syntegon believes the MLD Advanced deserves to be selected for a Technology Excellence Award at PACK EXPO.
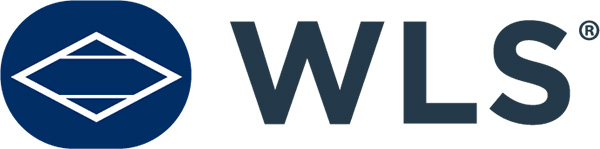
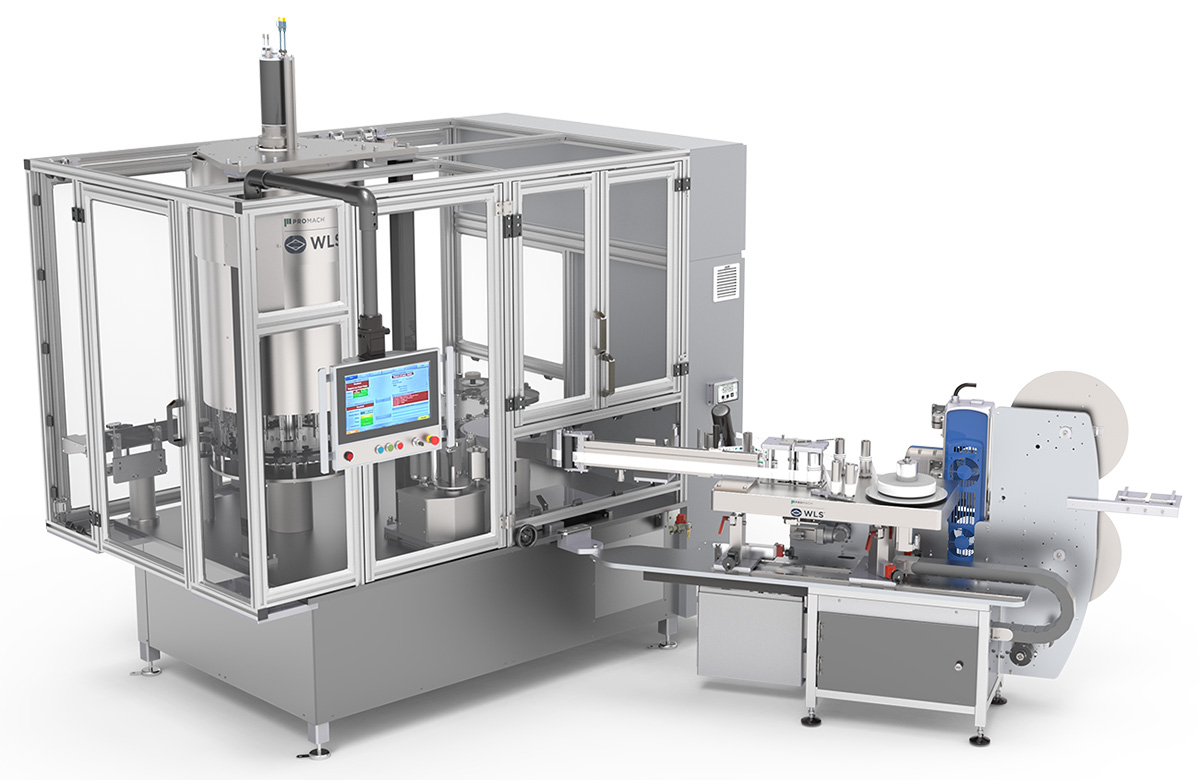
The NEW, patented PR-12 and PR-24 from WLS perform high-speed, high-control plunger rod insertion, and syringe labeling in one, single, compact-footprint unit.
The PR-12 is designed to run 300 bulk syringes per minute. The PR-24 is designed to run 600 bulk syringes per minute.
The system is designed to run the following syringe sizes: 0.5mL. 1mL short, 1mL long, 2.25mL, 3 mL and 5mL.
What makes your product or technology innovative?
The PR-12 and PR-24 from WLS feature our new, patented ATR Technology.
This unique, automated regulation of torque is what makes this plunger rod insertion machine a generational leap forward over prior plunger rod insertion technology.
The system will not disrupt the plunger height or seal while inserting the plunger rod.
The system is designed to compensate for a plunger placement tolerance of +/- 5mm. This ensures plunger rod is fully seated into the plunger every time.
This new cutting edge innovation provides greater control and greater protection of the aseptic seal created by the plunger.
------------------------------------------------
This innovation from WLS is a once-in-a-generation innovation and will truly raise the bar for quality in the insertion of plunger rods into syringes. Along with that, the unit utilizes WLS's tried and true vacuum drum labeling technology in the same compact unit. In consideration of the great technological leap this machine takes, we would very much appreciate consideration and nomination for this award.
Sustainability
-high-quality.jpg)
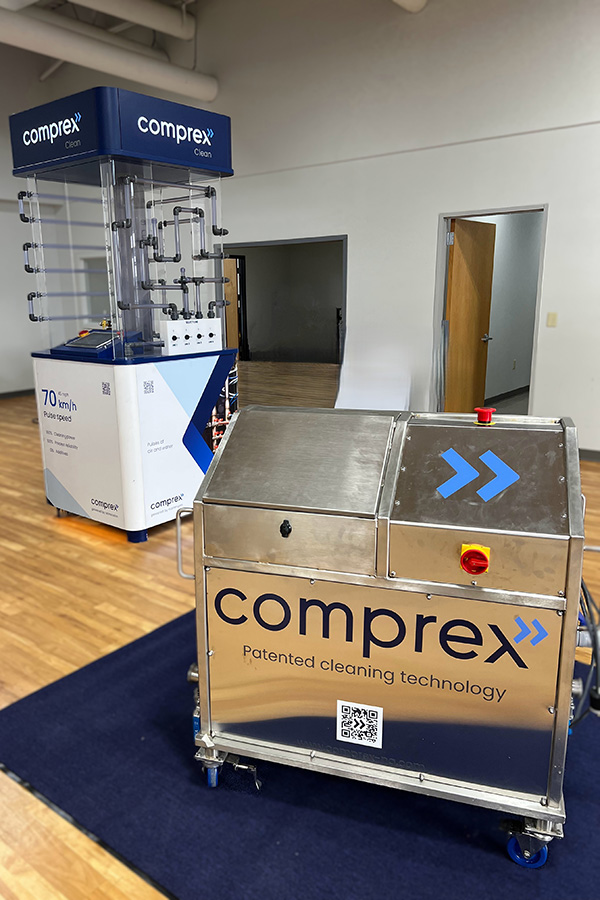
CIP- NEXT LEVEL CLEANING THAT IS REVOLUTIONARY!
At comprex®, we proudly uphold our commitment to the efficient and sustainable cleaning of piping systems and components.
We found our roots in municipal pipe cleaning in Germany over 25 years ago. Today, our services span a diverse spectrum of applications, extending beyond the municipal sector to encompass industrial, food and beverage, pharmaceutical, dairy, drinking water, and numerous others.
In addition to pipelines, our cutting-edge technology is designed to clean a variety of inline equipment, including heat exchangers, static mixers, and a wide range of inline process components.
The comprex® Impulse Cleaning Process operates through a mechanical approach, harnessing pulsed compressed air and minimal water usage. Our mission is to treat water as a precious resource, utilizing it responsibly and driving improvements in energy efficiency through our innovative CIP technology.
Hygiene is a critical aspect in numerous applications we serve. While our key differentiating factors include water, energy, and time savings, we also protect our customers from product loss due to microbial and quality issues stemming from unclean pipes, such as cross-contamination.
comprex® Impulse Cleaning provides excellent value for Clean-in-Place (CIP) services for most inline components, including heat exchangers. Our services enhance heat transfer efficiency while reducing downtime and maintenance requirements. By optimizing the cleanliness and functionality of inline components, we empower our clients to achieve peak performance and operational excellence.
When it comes to cleaning your pipeline (industrial, food and beverage, pharmaceutical, dairy, drinking water, and more), we employ our patented comprex® Impulse Flushing Process. This innovative method offers you an efficient, ongoing cleaning solution that reduces time, effort, and costs. It’s available for both preventive and remedial cleaning.
The powerful cleaning impulses generated by air and water are not only highly effective but also consume up to 90% less water compared to a traditional water flush. The mechanical cleaning forces applied to the internal surfaces of process lines and components are significantly amplified, reaching up to 100 times the strength of water rinsing when utilizing comprex®. Surprisingly, despite this intensified cleaning power, our process is gentle on the pipelines, as the pressure remains well below the system’s operating limits.
Comprex partners with a non-chemical called Virdivis an all-purpose cleaner, descaler, and degreaser.
- More Effective Cleaning – proven to remove build-up of gunk, slime, grime, and mineral deposits. Advanced technology for removal of biofilms and microbes
- Safe & Bioinspired – no harsh chemicals, safe for all metals, glass, plastics, elastomers, even evaporative pads. All ingredients on FDA GRAS (Generally Recognized as Safe) list
- Easy to-use in 1-step clean & remove for clean-in-place (CIP) and clean-out-of-place (COP)
- Less time and less manpower spent on cleaning resulting in significant cost savings
- Non-toxic and noncorrosive makes handling and storage easier
- 1-step cleaning means more effective cleaning. Less chemicals used means less cost and less waste disposal
Comprex and Viridivis deliver a dual-action cleaning solution—eliminating chemicals, reducing water use and downtime, and setting a new standard in CIP performance.
What makes your product or technology innovative?
Sustainability Benefits of Comprex:
Massive Water Savings
- Traditional CIP (Clean-in-Place) systems often use thousands of gallons per cycle.
- Comprex uses short, high-efficiency air and water impulses, often reducing water usage by up to 90%.
- Ideal for water-scarce facilities or those paying for purified water.
Chemical-Free Cleaning
- Comprex can clean without relying on harsh chemicals. This reduces:
- Chemical costs
- Chemical effluent
- Worker exposure risks
- Environmental discharge treatment
Lower Energy Demand:
- Less water = less need for waterheating.
- Less chemical usage = fewerenergy-intensive rinse cycles.
- Result: reduced thermal load on yourfacility.
Shorter Downtime = More Efficient Production
- Faster cleaning means less equipment idle time.
- Plants can run more efficiently, reducing waste from off-spec product starts or delays.
Extended Equipment Life
- Non-invasive, low-pressure impulses reduce:
- Metal fatigue
- Valve wear
- Pump abrasion
- Leading to longer asset lifespan and less replacement waste.
Comprex effectively dislodges residues without chemicals or mechanical intrusion. Paired with Viridivis, a biodegradable and low-foaming cleaning fluid optimized for rapid rinsing, we achieve superior cleaning with up to 90% less water, dramatically reduced downtime, and no reliance on traditional caustic or acid-based chemicals. This combination improves sustainability substantially.
Comprex = Less Water + Fewer Chemicals + Lower Energy + Less Downtime + Longer Equipment Life
It’s not just efficient---it’s a smarter, cleaner way to clean. With our comprex® process, we offer an effective, sustainable and efficient cleaning alternative.
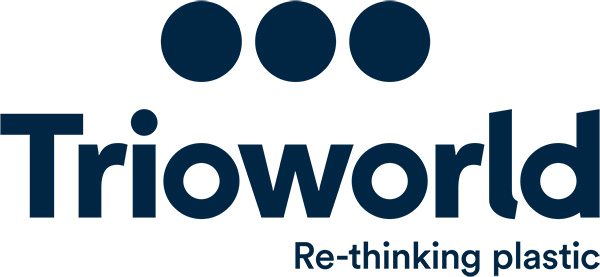
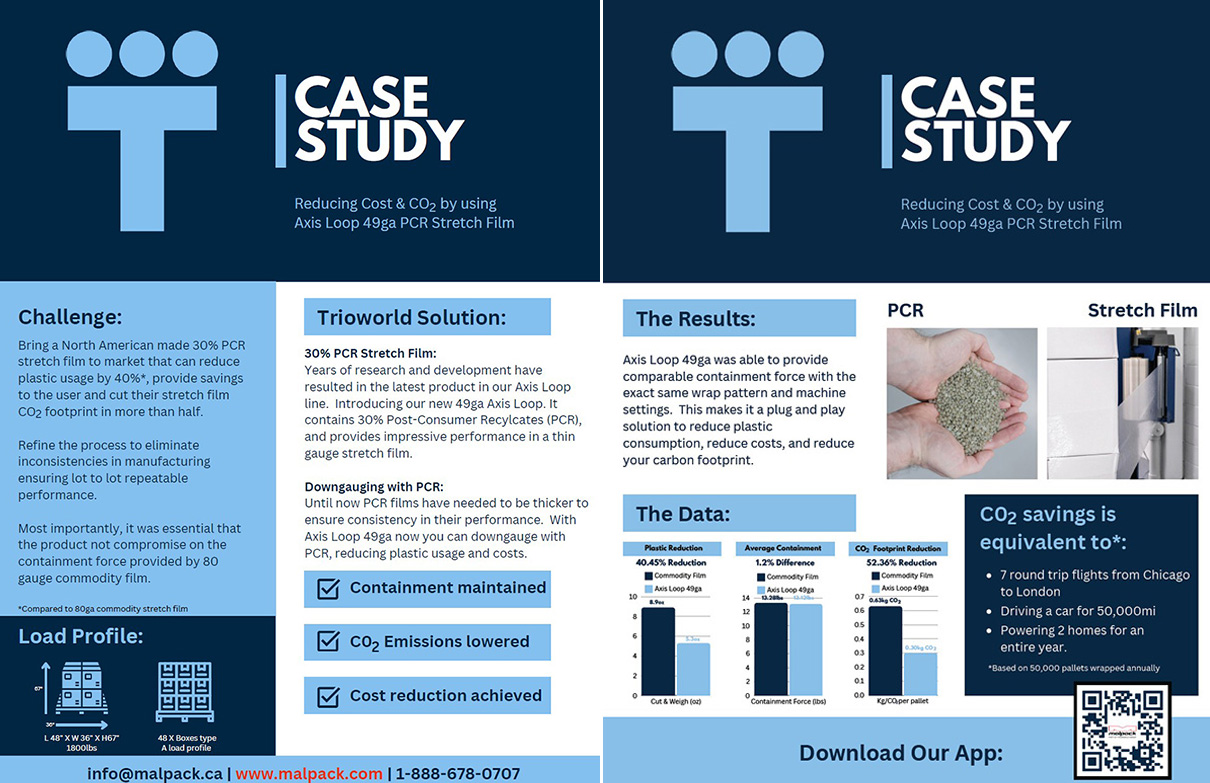
Trioworld’s Commitment to Sustainability and Circular Economy
At Trioworld, sustainability is at the heart of our operations. We are leading the packaging industry by offering innovative solutions that not only meet our customers' needs but also contribute significantly to a more sustainable future. Our focus is on creating products with reduced material usage and incorporating Post-Consumer Recycled (PCR) content, ensuring that our packaging solutions align with the principles of the circular economy.
Reducing Material Use and Incorporating PCR Content
One of our key sustainability goals is to minimize the material used in packaging. Trioworld’s high-performance films are thinner and stronger, allowing customers to use less material while maintaining the required strength. This reduction in plastic usage is essential for decreasing plastic waste and its environmental impact.
We also prioritize using PCR content in our products. Our films contain a minimum of 30% certified PCR, helping reduce the reliance on virgin plastics and lowering CO₂ emissions by up to 50%. Trioworld ensures that all our products are designed for recycling, ensuring they can be reintegrated into the circular economy.
Circular Film Solutions and Baled Film Collection
We offer circular film solutions containing at least 30% PCR content without increasing the cost for our customers. In addition to offering sustainable products, we help close the loop by providing a Baled Film Collection program. This service enables the collection and recycling of used films, reducing the need for disposal and promoting sustainability.
Our partners, accredited by the Association of Plastics Recyclers, help us sort and clean the collected material. The material is then transformed into high-quality PCR regranulate, which can be used again to create new products, completing the circular process.
A True Circular Solution
Trioworld’s circular approach ensures that plastic materials are restored, recycled, and reincorporated into new films. We are committed to supporting a circular plastics economy by offering high-performance, recyclable packaging solutions that help our customers reduce their environmental impact.
EcoVadis Platinum Rating
Trioworld's sustainability efforts have been recognized globally with the EcoVadis Platinum Rating, placing us in the top 1% of over 100,000 companies assessed worldwide. This award reflects our commitment to maintaining sustainable practices across all aspects of our business, from product design to operations. We work closely with our customers to help them adopt sustainable packaging solutions that align with their environmental goals, including the integration of PCR content.
What makes your product or technology innovative?
Why Trioworld’s Product is Truly Innovative
Trioworld’s commitment to sustainability and innovation is exemplified in our high-performance stretch films, which are designed to meet the evolving needs of both our customers and the planet. What sets our product apart is its combination of reduced material usage, 30% Post-Consumer Recycled (PCR) content, and exceptional performance, making it a leader in the circular economy for flexible packaging.
Our stretch films are thinner and stronger, allowing for reduced material usage without compromising durability or load stability. This innovation helps businesses cut down on plastic waste, while still maintaining the necessary performance standards for their packaging needs. By offering films with PCR content, we are not only reducing the dependency on virgin plastics but also decreasing carbon emissions, making a significant contribution to environmental preservation.
What truly makes our product innovative is the seamless integration of circularity into every step. We don’t just provide sustainable products – we enable our customers to be part of the solution. Our Baled Film Collection program allows for used stretch films to be collected, sorted, cleaned, and recycled back into the product line, closing the loop of the plastic lifecycle. This process results in the creation of high-quality PCR regranulate, which can be reused, reducing waste and promoting a circular packaging solution.
Trioworld's stretch films embody the future of sustainable packaging, combining environmental responsibility with high performance, and offering a tangible solution that supports a truly circular economy.

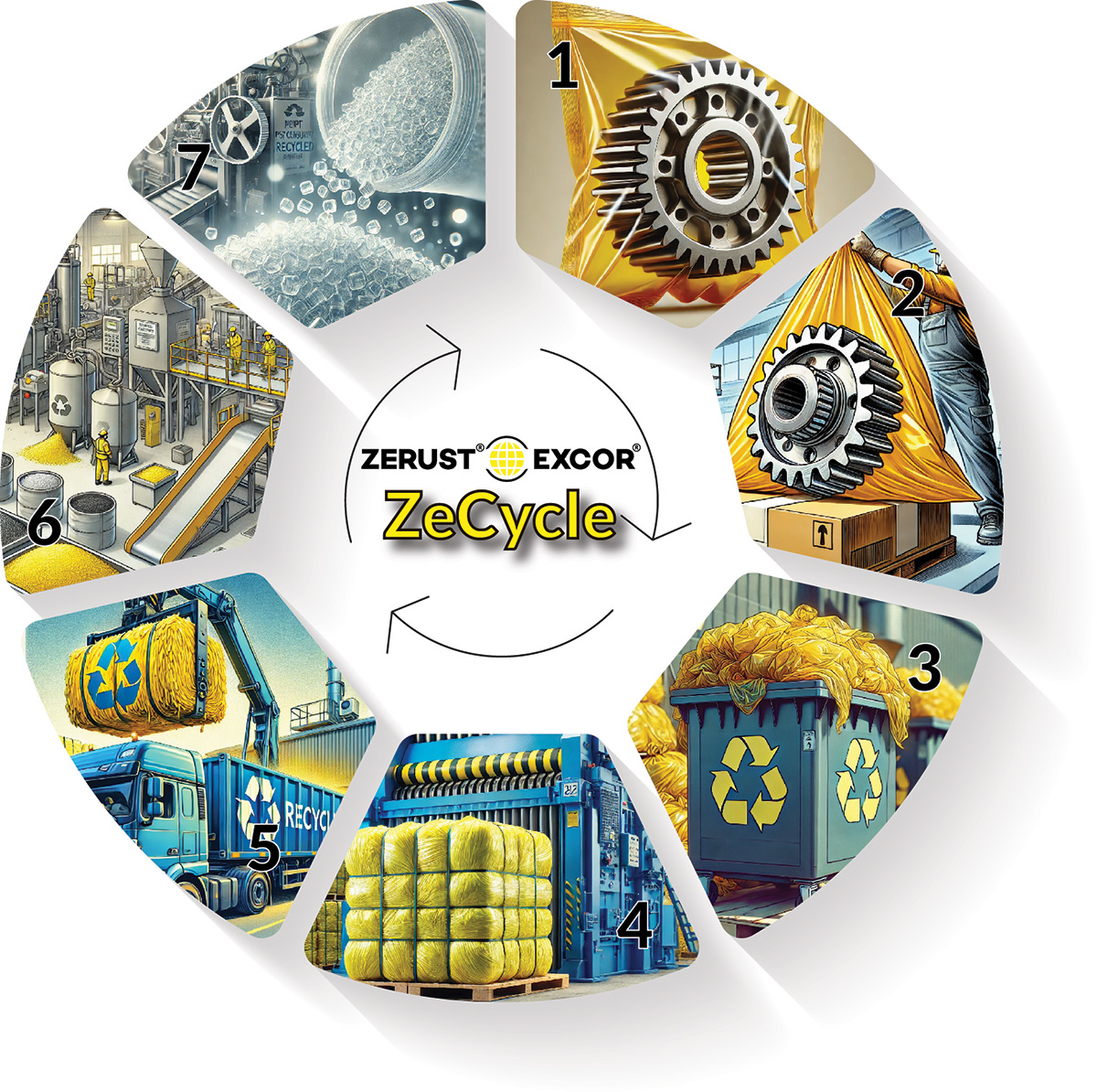
ZeCycle is an innovative closed-loop recycling program developed by ZERUST in partnership with RecycleMax, designed to help industrial manufacturers reduce plastic waste and carbon emissions. This program enables companies to collect and recycle used ZERUST VCI packaging and plain LDPE poly films, which are then processed into post-consumer recycled (PCR) resin and used to manufacture new ZERUST ICT510-PCR30 VCI film. By transforming end-of-life packaging into new corrosion-inhibiting film, ZeCycle advances sustainability goals, supports a circular economy, and provides a measurable environmental impact, offsetting approximately 1,480 lbs of greenhouse gas emissions for every 1,000 lbs of film recycled.
What makes your product or technology innovative?
ZeCycle revolutionizes sustainability in industrial packaging by combining proven VCI technology with a seamless recycling process never before introduced at PACK EXPO. Unlike traditional recycling methods, ZeCycle is a fully integrated program that includes film collection, baling, transport, reprocessing, and reintegration into new protective packaging—all tracked through RecycleMax’s real-time data platform. This gives customers measurable insight into their environmental performance. ZeCycle not only minimizes waste and emissions but also creates a closed loop for industrial packaging in a scalable, efficient, and impactful manner, making it a leading example of sustainable innovation in the packaging industry.